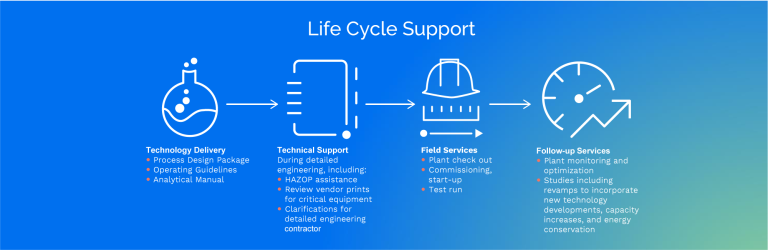
Technology Delivery
Process Design Packages (PDPs)
The primary vehicle for delivering technology to a licensee is the PDP. The contents of these packages are flexible and tailored to meet the licensee's requirements. The PDP contains everything necessary to deliver the technology to the client in order to proceed to the detailed engineering phase of the project. This includes among other things, process flow diagrams (PFDs), heat and material balances, equipment list, piping and instrumentation diagram/drawings (P&IDs), equipment data sheets, and plot plan.
Operating Guidelines
The second main vehicle for technology delivery is the Operating Guidelines, which provide licensees sufficient information to produce Standard Operating Procedures in their standard format.
Analytical Manual
The Analytical Manual addresses testing of feedstocks, internal process streams, product, and waste streams. A summary provides identified streams to be sampled, recommended test methods, key compositions, and sampling frequencies for startup and normal operation. A recommendation of key analytical equipment is included.
Training
Licensee training is typically completed in three parts:
- Classroom Training: Badger's training advisors provide classroom training for the licensee's staff. Training manuals, drawings, and other training materials will be prepared by Badger and given to the licensee's staff.
- Training at a host plant: Badger's training advisors will accompany the licensee to the host plant to co-ordinate the training activities. During the training sessions, Badger will highlight differences in equipment, layout and performance between the licensee's plant and the host plant.
- Training at a host laboratory or Badger's laboratory: licensee's analytical chemists will be trained in analysis and testing procedures.
Operating Guidelines - A Closer Look
- Operating guidelines typically contain the following sections:
- Overview
- Process description
- Initial startup
- Normal operation (includes normal startup, normal operation and normal (planned) shutdown activities)
- Emergency shutdown procedures (address utility failures, equipment failures, and process anomalies)
- Special systems & procedures
