Cumene Technology

Badger Cumene technology has gained worldwide acceptance as the standard for production of cumene. Our cumene technology results in a high yield, highly energy efficient, and low environmental impact process. It is easy to operate and maintain and offers low capital and operating costs. Badger and ExxonMobil share a 25-year history of cooperation in the development of catalysts and processes for the production of cumene from polymer grade, chemical grade, and refinery grade propylene.
A fixed-bed catalytic alkylation reactor system converts benzene and propylene to cumene in the liquid phase. Proprietary zeolite catalysts available through ExxonMobil are used for the reaction. The technology is flexible and can produce cumene from a variety of propylene sources including refinery, chemical and polymer grades.
The conversion of propylene is typically higher than 99.999%, and the yield loss is typically less than 0.3% of the total raw materials consumed. Product purity above 99.97% weight has been regularly achieved in commercial operation. Benzene in stoichiometric excess is required for cumene synthesis; the excess benzene is recovered by distillation and recycled to the reactors.
The cumene process licensed by Badger uses an extremely low benzene to propylene (B/P) ratio in the alkylator feed and an extremely low benzene to PIPB ratio in the transalkylator feed, resulting in very low equipment cost and energy consumption. The ExxonMobil catalysts are noncorrosive, environmentally inert, and regenerable. These catalysts are free flowing before and after use and require no special packaging or handling. Offsite regeneration is typically the preferred method due to the long cycle length. These catalysts also enable the bulk of the plant to be constructed of carbon steel. The catalyst does not produce byproduct oligomers.
Commercial Experience
- As of early 2024, plants using our Cumene technology produce over half of the world’s cumene capacity having a total installed capacity of more than 12 million metric tons per year.
- We have licensed and demonstrated single train capacities as large as 750 KTA.
- Our technology can produce high quality cumene from any commercial grade of propylene.
- We have successfully supplied cumene to all major downstream phenol processes.
Resources
The Cumene Process
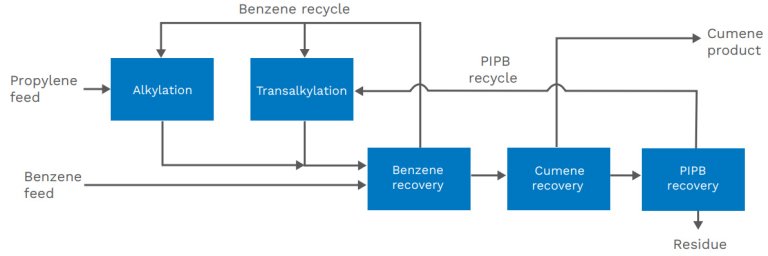
ALKYLATION
An alkylation system converts benzene and propylene to cumene. A small fraction of the cumene is further alkylated to polyisopropylbenzenes (PIPB). The alkylation reaction is exothermic and the alkylation reaction system is staged with intermediate cooling to control the reaction temperature.
TRANSALKYLATION
A single bed transalkylation system converts PIPB with benzene to additional cumene. Transalkylation is isothermal.
PURIFICATION
A distillation train recycles excess benzene to reactors, isolates cumene as product, and recovers PIPB for transalkylation.
The Badger Cumene process is a high yield, high energy efficiency, low environmental impact process that is easy to operate and maintain, allowing for very low production cost.